
Los tipos de acabados y cómo realizarlos
El abrasivo es una herramienta imprescindible para los acabados superficiales en piezas metálicas, y más concretamente, el abrasivo flexible. Un abrasivo de calidad es clave para conseguir buenos acabados consistentemente de una manera fácil y rápida. La tecnología de los abrasivos especializados permite ahorrar pasos, y además las lijas son más fáciles de usar, puesto que cortan mejor el material. A continuación, se explican todos los detalles que necesitas saber sobre los tres diferentes acabados: el acabado pulido espejo, el acabado satinado y el acabado vibrado.
La preparación superficial para un buen acabado
Desbaste, afinado y acabado o grano grueso, grano medio y grano fino. Esta es la secuencia, ya sea en manual o en automático. Tres pasos, los cuales se apoyan unos en los otros.
Primer paso: el desbaste
El desbaste es como la base de una pirámide: debe ser robusta y amplia para poder soportar el resto de las piezas que forman la pirámide hasta la cúspide, que sería ese pulido espejo o ese satinado uniforme. Si el desbaste no es bueno, el acabado no será bueno. Ahora bien, ¿qué es un buen desbaste?
Un buen desbaste es el que elimina los fallos superficiales del metal dejando una superficie homogénea. Ejemplos de estos fallos hay muchos, arañazos, golpes, proyecciones o incluso la capa superficial endurecida de los procesos de laminado de los aceros inoxidables.
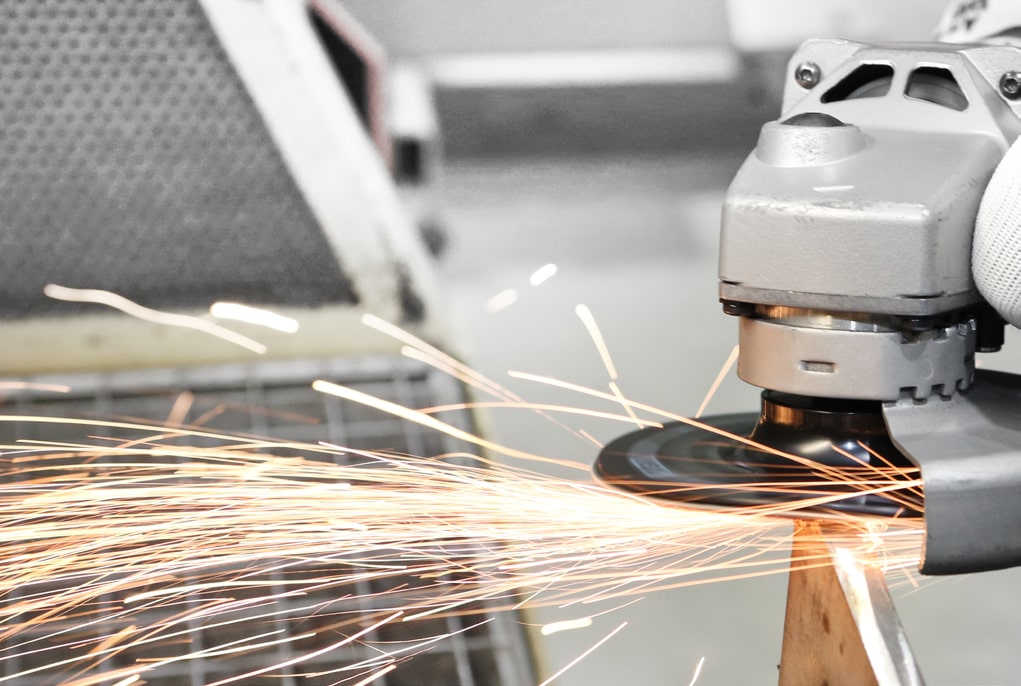
Eliminar los fallos superficiales con calma y a conciencia evitará muchos problemas posteriores. Es siempre mejor trabajar bien la pieza al principio que tener que volver a lijar la pieza porque se ven marcas de fondo indeseadas en el acabado. Es muy importante también tener cuidado con las marcas de temperatura. Al trabajar con granos abrasivos bastos que quitan mucho material, es posible decolorar la pieza. Para evitar estos problemas, un abrasivo de calidad facilita mucho las cosas.
Segundo paso: el afinado
La misión en este paso es rebajar la rugosidad superficial pico-valle. El desbaste sería como el arado que labra la tierra y el afinado sería el rastrillo que rebaja los surcos que deja el arado. Este ejemplo gráfico es muy importante para entender la diferencia entre un abrasivo de calidad para el afinado y uno que no lo es. El abrasivo de calidad rebaja los surcos del desbaste eliminando metal de los picos creando microsurcos como hace un rastrillo. Un abrasivo que no sea bueno simplemente aplasta los picos dejando mesetas con valles entre ellas que nunca se podrán eliminar con granos más finos, porque se toparán con esas mesetas.
Casi todos los problemas de marcas de fondo que se puedan encontrar vienen de este paso. Para el afinado es importante pensar en hacer mejor saltos de grano pequeños que después tener piezas con problemas de calidad. Como máximo no se deben hacer saltos de grano superiores a tres niveles de grosor, sin embargo, si nos movemos entorno al grano #120 es mejor hacer saltos como mucho de dos granos. Esto es debido a que es crítico tener una buena base para que los granos finos y muy finos trabajen bien.
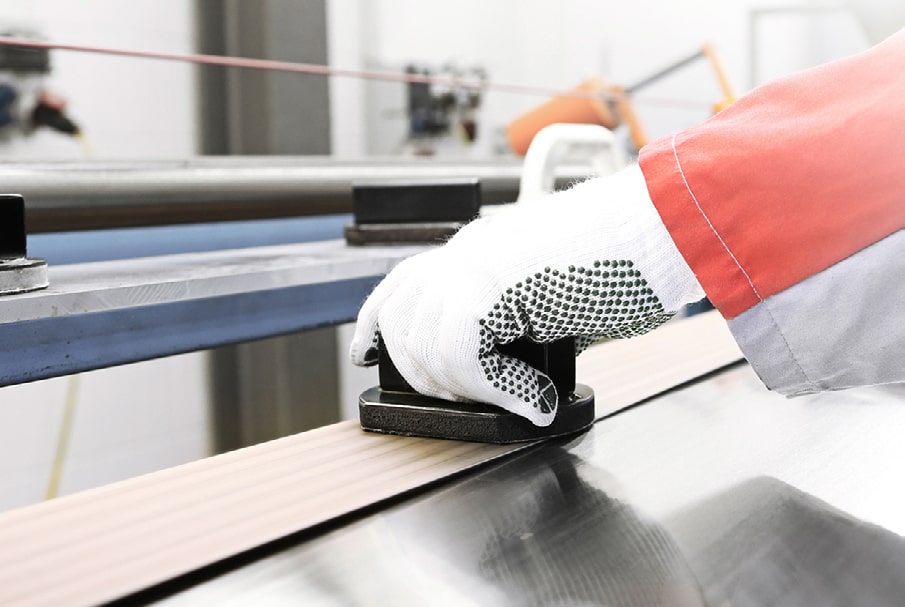
Tercer y último paso: el acabado
Este es el último paso de todos. En esta etapa no se pueden arreglar fallos que se arrastran del afinado o del desbaste. No vale la pena perder tiempo intentando eliminar fallos con los granos muy finos, es siempre mejor volver algún paso atrás. Los abrasivos para los acabados finales suelen ser también más caros y de menos durabilidad por ello, por lo que para mejorar la eficiencia del proceso es muy recomendable hacer un buen desbaste y afinado antes de realizar el acabado.
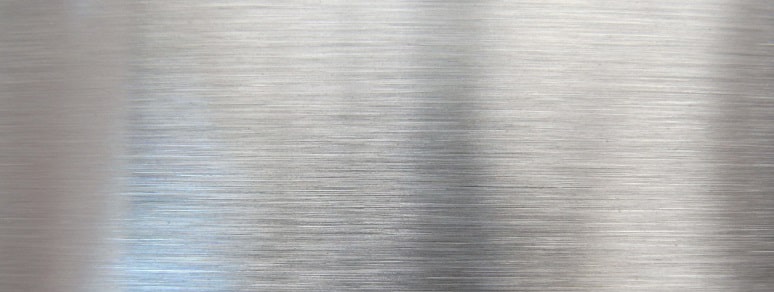
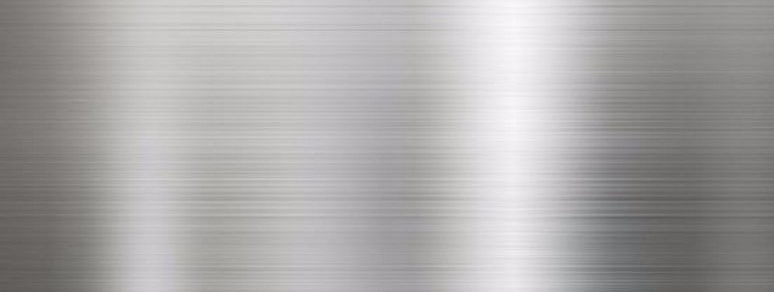
Consejos según el acabado que se busque
Acabado pulido espejo
Los acabados espejo sobre superficies metálicas son generalmente en acero inoxidable, aunque es posible pulir a espejo otros metales como latón o algunos aluminios. Por regla general, los pulidos se hacen a mano con máquinas portátiles por lo cual es uno de los acabados más caros que hay. Existe una técnica que ayuda a homogeneizar la pieza y ganar calidad en el pulido que consiste en cruzar 90º el sentido de lijado.
Se lija de izquierda a derecha y después de arriba abajo para romper la dirección de la rugosidad superficial, ya sea usando el mismo grano o en el paso de un grano al siguiente. Una superficie afinada de esta forma dará como resultado un pulido espejo uniforme desde cualquier perspectiva, ya que el pulido no es un acabado direccional. Si solo se lija en una dirección, es posible que la superficie no se refleje como en un espejo si el punto de vista es perpendicular a la dirección de lijado.
También existen pulidos espejo con máquinas automáticas y bandas de lija. Estas bandas son por regla general bandas de corcho con abrasivos por encima que dejan un brillo espectacular en pocas pasadas. Esta es la solución idónea para piezas largas, como pueden ser tubos o pletinas finas si las exigencias de calidad del pulido final no son muy altas, ya que es un pulido de mucho brillo pero que deja bastantes fallos o pequeños arañazos a la vista.
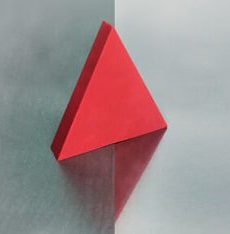
Acabado satinado
El satinado, en contraposición con el pulido, es un acabado direccional. Los destellos de la superficie van en una dirección y dan una sensación como la de un cielo con estrellas fugaces. Esta direccionalidad hace que este acabado esté orientado hacia las máquinas automáticas y mucho menos a las aplicaciones manuales, justo al contrario que los pulidos. Sin embargo, este artículo trata de la calderería fina y por ello se centrará en las múltiples aplicaciones de satinado manuales que existen. Las herramientas específicas para satinar una superficie son los rodillos o tambores de lija abrasiva para máquinas portátiles como en la siguiente imagen:
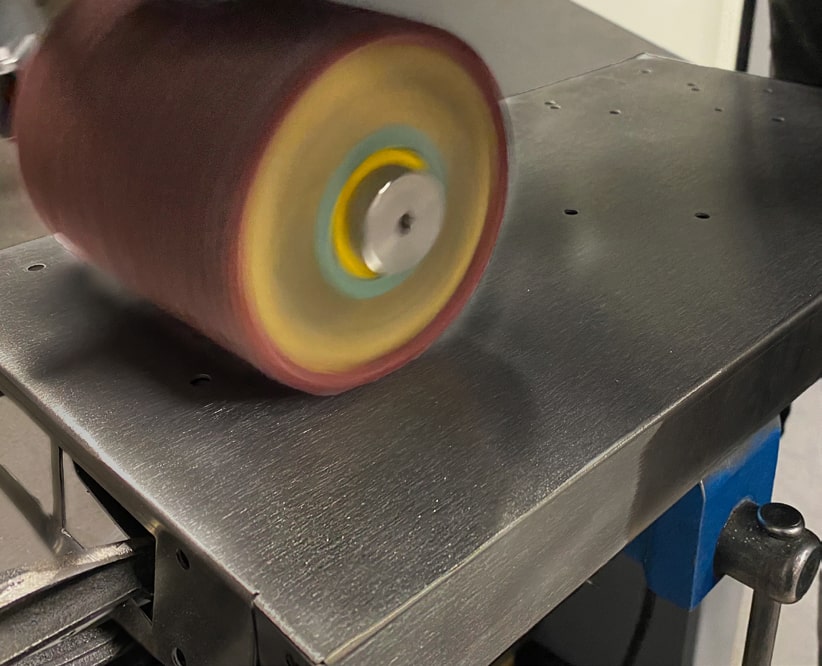
Otra herramienta muy útil para el satinado de piezas manejables es una lijadora de banda larga, la cual permite un amplio juego de posibilidades con varios elementos de contacto y velocidades variables. Un consejo valioso en este tipo de superficies, es el uso de máquinas con velocidades ajustables, ya sea en máquinas portátiles o en banda larga, para poder modificar el largo de la marca del satinado y así diferenciarse de la competencia. Quizá el satinado sea (de los tres acabados descritos en este artículo) el más extendido en el mercado, por eso es importante tener presente la importancia de la diferenciación de la competencia.
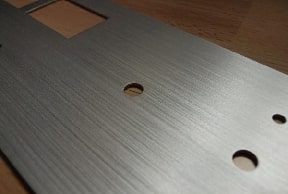
A pesar de ser un acabado menos exigente que el pulido, también hay que tener mucho cuidado en el desbaste y el afinado porque la belleza del satinado reside en la uniformidad. Las marcas profundas crean una disonancia desagradable y también pueden dar problemas de oxidación o deterioro prematuro del acabado.
Acabado vibrado
Este acabado es el más sencillo de los tres, y el menos extendido también. Es un acabado manual no direccional que consiste en el uso de una lijadora excéntrica con un grano P60, aproximadamente, para obtener líneas curvas similares a “caracolillos”, para después repasar esa superficie con un vellón dando lugar al acabado vibrado. En la siguiente fotografía se encuentra un ejemplo de este acabado:
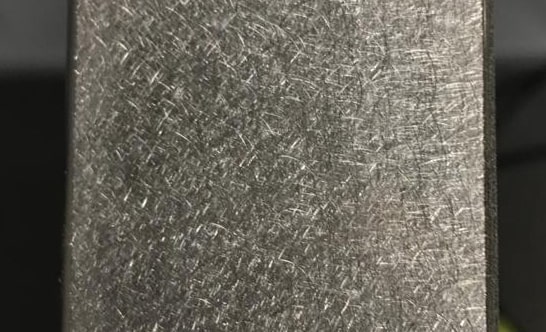
La principal ventaja es la sencillez del proceso la cual evita tener que formar a operarios durante mucho tiempo. Otra gran cualidad es que es un acabado que no cambia con el tiempo, envejece bien. En contrapartida, no es muy fino y estético por lo que las aplicaciones que acepten este tipo de acabados son pocas.
Cómo escoger un abrasivo adecuado
En este caso, solo se nombrarán soluciones en abrasivos flexibles, ya que son los más adecuados y los más extendidos para este tipo de tareas en la industria metalúrgica.
El desbaste es común a todos los acabados, la misión es igualar toda la superficie y por eso es importante tener una herramienta abrasiva que corte bien el metal y que no lo aplaste o deforme en lugar de arrancar viruta de toda el área por igual. El grano abrasivo cerámico es el mejor para el desbaste sin lugar a duda. En
esta categoría de abrasivos cerámicos hay dos posibilidades diferentes, granos de forma triangular definida o granos irregulares puntiagudos. El rendimiento de los granos triangulares es muy alto respecto a los granos cerámicos tradicionales que también tienen, por su parte, una muy buena relación calidad-precio todavía.
A la hora de escoger el abrasivo no solo el grano es importante, también lo son las condiciones en las que se va a lijar. Si el proceso es seco, lo mejor es usar abrasivos con TopSize, que es una capa extra refrigerante.
Por lo contrario, si el proceso es en mojado, lo más adecuado es usar abrasivos sin esta tercera capa que puede llegar a ser contraproducente en estas
aplicaciones.
En cuanto al afinado, es necesario diferenciar entre el afinado para un pulido y para un satinado. Para los pulidos se usan, por regla general, abrasivos multicapa con gránulos o abrasivos estructurados. Para los satinados lo que se usa son los abrasivos multicapa con gránulos o vellón abrasivo más conocido como vellón.
Los abrasivos standard, en este tamaño de granos finos o muy finos se descartan porque tienen una corta durabilidad, lo cual provoca muchas pérdidas de tiempo por el cambio constante de la lija y también más gasto en abrasivo. Un proceso de afinado optimizado no usa abrasivos standard por regla general.
La oferta para realizar un satinado final es amplia. Rodillos, bandas abrasivas de granos multicapa y “surface conditioning material” de vellón abrasivo son las principales alternativas. La siguiente tabla refleja el tipo de acabado que deja cada una de estas herramientas abrasivas:
ABRASIVO | PRESIÓN SOBRE EL GRANO | ANCHO DE MARCA | ACABADO SOBRE EL GRANO |
Rodillos C&F | Baja | Medio | Mate |
Rodillos de lija | Media-Baja | Fino | Mucho brillo |
Gránulos de grano abrasivo | Alta | Ancho | Brillo |
SCM | Media | Medio-Ancho | Mate |
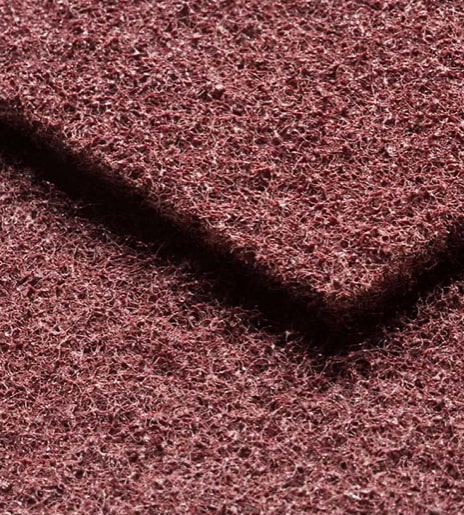
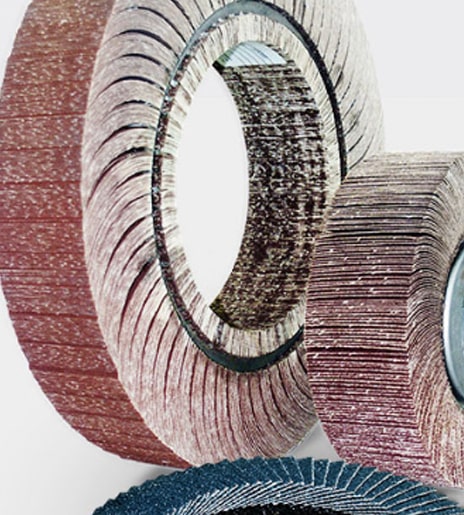
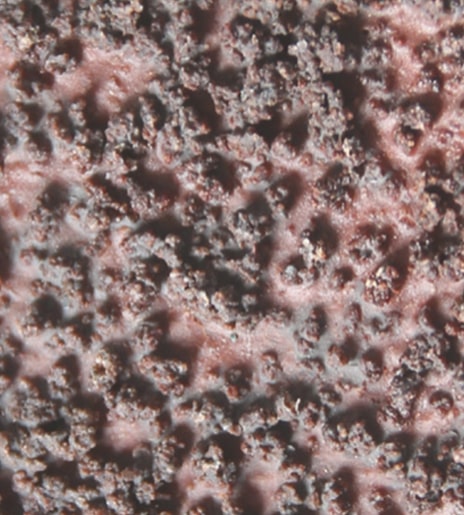
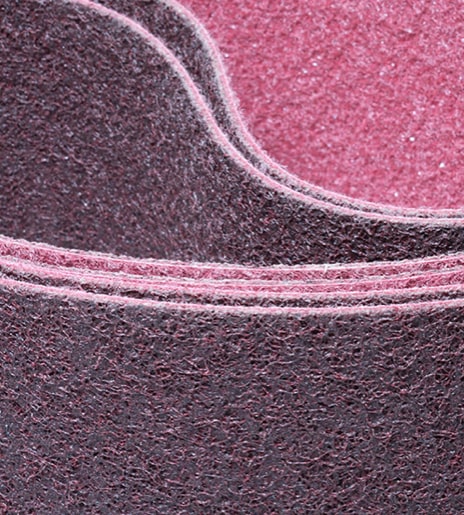
Problemas habituales en los acabados y cómo resolverlos
Rayas de fondo
Las rayas de fondo son profundos valles que quedan entre mesetas de rugosidad superficial. Es un problema más particular de los pulidos, pero también pueden estropear la uniformidad de los satinados. La solución a este problema es siempre preventiva porque si aparecen, hay que volver a lijar toda la pieza.
Para evitar este tipo de problema se deben utilizar abrasivos de corte como son abrasivos multicapa y no vellones abrasivos, los cuales aplastan más la superficie que la lijan. Arrancar viruta es la mejor señal de que se está realizando un buen trabajo y esa viruta también debe ser apreciable en los granos más finos. La señal de que un abrasivo está desgastado no es solamente su aspecto, si no el arranque de viruta que se puede comprobar limpiando la pieza antes de lijar y ver si después de lijar se encuentran restos de metal.
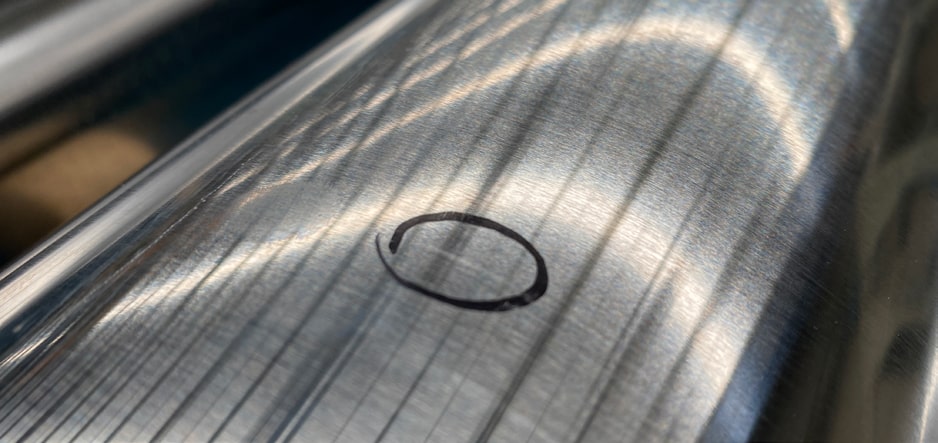
Decoloración o marcas de temperatura
La temperatura excesiva es consecuencia de una alta velocidad relativa entre el grano abrasivo y la pieza en la mayoría de los casos. Es decir, que la lija vaya a mucha velocidad y que la pieza no se mueva o se mueva muy lenta. Las decoloraciones pueden llegar a ser peligrosas a nivel estructural, y a nivel estético, muy difíciles de rectificar.
Para evitar este tipo de fallos lo mejor es reducir la velocidad de corte de la máquina y aumentar la de avance, que en caso de una radial sería mover la máquina más rápido por la pieza. En el caso de que esto no sea posible y se esté trabajando en seco, los productos con Top Size o con otros recubrimientos ayudan a evitar quemar la pieza. Además, también está la posibilidad de trabajar bajo niebla o mojar la pieza antes de lijar, ya sea con agua o con una gota de aceite.
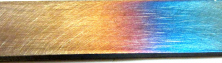
Las esquinas o ángulos
Este problema es típico en satinados manuales por ser direccionales. Por regla general, lo que se hace en los cruces de dirección de satinado, por ejemplo, al satinar el marco de una mesa, es proteger el vértice con cinta y lijar en una de las direcciones. A continuación, se protege el vértice por la parte ya satinada y se satina la dirección restante. Así, el cruce será justo en el vértice, quedando estéticamente muy vistoso, puesto que todas las marcas de cada uno de los satinados paran justo en el vértice, dejando una línea perfectamente apreciable como en la siguiente ilustración.
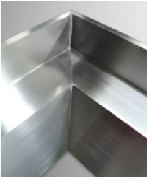
Para afinar más los acabados no es recomendable trabajar más con los granos muy finos o super finos, si no dar más pasos intermedios en el afinado. El rebaje de la rugosidad superficial minimizando la altura pico-valle con granos muy finos no es posible, esta es la misión de los granos medios que posibilitan después que el acabado sea mejor.
Es el caso específico del satinado, si se quiere mejorar, lo ideal es satinar sobre una superficie más fina que el grano del satinado final. De esta forma, se imprimirá justamente el grano del satinado requerido dejando la superficie mucho más uniforme.
Autor: VSM